
Newsletter
Bleiben Sie verbunden
Bleiben Sie mit unseren Newslettern auf dem Laufenden! Informieren Sie sich über die neuesten Softwareversionen, tauchen Sie ein in die innovative Ermüdungsanalyse mit FEMFAT, entdecken Sie spannende Veranstaltungen und Schulungsmöglichkeiten und erkunden Sie fesselnde Fallstudien. Wir beantworten auch gerne Ihre häufig gestellten Fragen. Entdecken Sie die Welt der technischen Spitzenleistungen!
Zum Newsletter anmelden
Newsletter 33/2025
Release News: FEMFAT inside Ansys v4.11, Indian User Meeting 2025 Recap, Magna ECS Simulation Conference, Events & Trainings, Technical Article: Transforming Pulsating Load Test Data into Alternating Strength Data for FEMFAT, Release FEMFAT LAB 2025, 2 FAQs
Introducing FEMFAT inside Ansys v4.11
We are excited to announce the release of FEMFAT inside Ansys v4.11, now compatible with ANSYS 2024 R2 and ANSYS 2025 R1. This latest version brings a host of new features and improvements designed to streamline your workflow and enhance your simulation capabilities.
Key Updates in FEMFAT inside Ansys v4.11:
1. Support for Weld Definition Files (*.wdf):
You can now import Weld Definition files directly into your analysis, making it easier to integrate welding data into your simulations.
2. Enhanced Message File Functionality:
The Message File, which contains all warnings and errors from FEMFAT runs, has been upgraded. You can now highlight elements related to specific warnings and errors directly in the Geometry window. This feature allows you to quickly localize and address issues within your model, potentially filtering them by damage or endurance safety factor values. The search functionality in the Worksheet window (accessible via CTRL+F) has also been implemented for the Message File object.
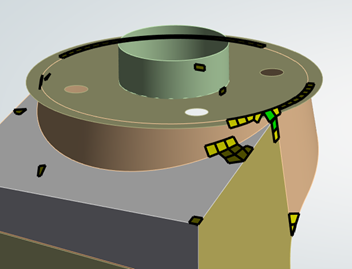
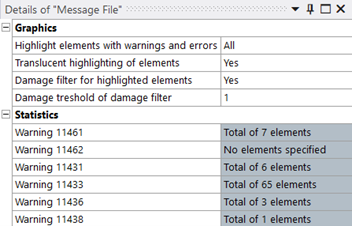
3. One-Click Insertion of Analysis Result Objects:
Simplify your workflow with the new one-click option to insert all available result objects of an analysis at once. This feature is accessible via the FEMFAT toolbar.
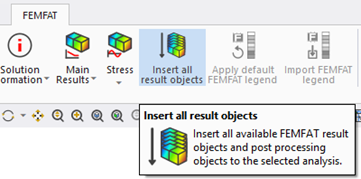
4. Direct Renaming of Analyses:
You can now rename analyses directly within the Mechanical Tree, providing greater flexibility and organization in your projects.
5. Copy/Paste Material Data and Node Characteristics:
The ability to copy and paste Material Data and Node Characteristics across different analyses has been added. This functionality allows you to efficiently transfer data between analyses using the Copy and Paste buttons in the FEMFAT Toolbar.
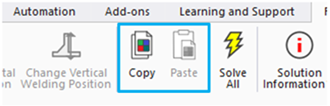
These enhancements are designed to provide you with more efficient tools for your structural mechanics simulations, ensuring that you can focus on what matters most—delivering accurate and reliable results.
A look Back at the 7th Indian FEMFAT User Meeting in Pune
On March 6, 2025, the 7th Indian FEMFAT User Meeting took place at the magnificent Hotel Sheraton Grand in Pune, India. This prestigious event drew around 170 participants from various sectors of the engineering community, providing a vibrant platform for professionals to exchange expertise and experiences in the field of durability analysis. With 15 external presentations and the latest FEMFAT features showcased by ECS, the meeting was a resounding success.
Event Highlights:
The event featured a diverse range of topics, including weld and spot analyses, components under thermal load, elastomers, material data, benchmark studies, and drivetrain components. Notable presentations included success stories from TATA and VECV on weld and spot analyses, thermomechanical analysis of a cylinder head by TATA, and shape optimization of a piston by Wabtec. Mahindra Swaraj captivated us with their simulation of a shaker test for a tractor fender, Knorr Bremse impressed with a FEMFAT analysis of the compressor crankcase and air dryer housing using SPECTRAL, and Mercedes wowed us with their analysis of an oil pan on the differential housing. The discussions covered a wide array of applications, from sports cars and heavy commercial vehicles to locomotives and motorcycles.
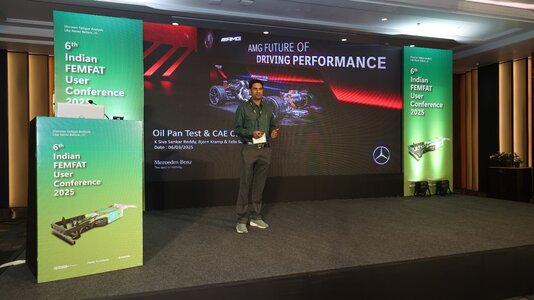
A key highlight was the presentation of the Best Lecture Award, selected by a three-member expert jury. This year, the award went to TATA for their thermomechanical evaluation of a cylinder head using FEMFAT heat. This winning presentation will also be featured at the international FEMFAT User Meeting during the Magna ECS Simulation Conference on May 14-15, 2025.
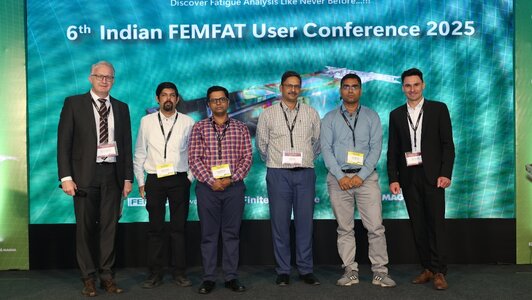
Winners of the best lecture award from Tata Motors
This conference was not just an event; it was a celebration of innovation, collaboration, and the relentless pursuit of excellence in fatigue analysis. Participants had the opportunity to network with industry leaders, share insights, and explore the latest advancements in FEMFAT software. The energy and enthusiasm were palpable, making it clear that the Indian FEMFAT User Conference is a cornerstone event for anyone involved in fatigue analysis.
We look forward to seeing you at the next Indian FEMFAT User Conference, where we will continue to push the boundaries of what is possible in fatigue analysis.
Invitation to the upcoming Magna ECS Simulation Conference: Featuring FEMFAT
We are excited to invite you to our upcoming Magna ECS Simulation Conference 2025 , taking place from May 14 to 15 at "Das Schloss an der Eisenstraße".
This conference offers an excellent opportunity to learn about the latest developments and trends in simulation, fatigue analysis, and life prediction, and to network with industry experts.
Get your Conference Ticket
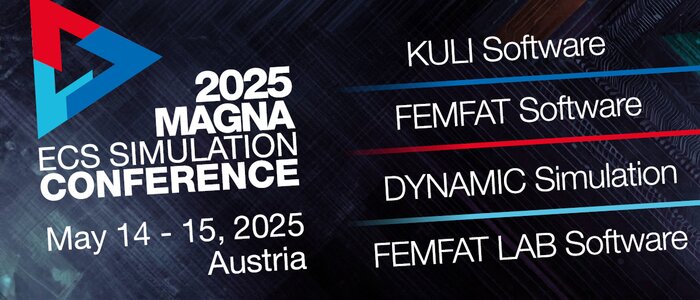
Agenda FEMFAT
May 14 | May 15 | |||
09:45 CEST | Welcome address | 09:00 CEST | Lightweight design enabled by innovative CAE-based development method combining fatigue life analysis and topology optimization | |
Werner Dantendorfer Magna Powertrain Engineering Center Steyr | Yoshiya Kato, Toyota Motor Corporation | |||
10:00 CEST | Introduction of software solutions and products | 09:30 CEST | Prediction of fatigue life of welded chassis components with structural stress method | |
Dipl.-Ing. Istvan Soproni, Cosma Engineering Europe Gmbh | ||||
11:00 CEST | Introduction | 10:00 CEST | Best lecture presentation, Usermeeting India | Advanced thermomechanical fatigue simulation of engine cylinder heads using FEMFAT HEAT - Sehitoglu Framework | |
Dipl.-Ing. Helmut Dannbauer and Dipl.-Ing. Klaus Hofwimmer, Magna Powertrain Engineering Center Steyr | Sunil Ghotekar and Dipak Kumbhar, Tata Motors Ltd. | |||
11:15 CEST | Plenary lecture - FEMFAT: Fatigue life prediction for composite laminates including damage mechanisms and stiffness degradation | 11:00 CEST | Strength design technology to efficiently ensure long-term reliability of electrical products | |
Dr. Clara Schuecker, Montanuniversitaet Leoben | Jun Morimoto, Toshiba Tec Corporation | |||
12:00 CEST | Development of the aluminum arc welding database and its application to vehicle development | 11:30 CEST | Using elastoloads for the transient fatigue analysis of wheel hub drives | |
Yuri Ichikawa and Chihiro Wada, Toyota Motor Corporation | Marton Graf, GDELS-Mowag | |||
14:00 CEST | FEMFAT 2025 news and more | 12:00 CEST | Fatigue damage estimation of vibratory structures under non-stationary loading using the DGP method and FEMFAT | |
Dr. Christian Gaier, Magna Powertrain Engineering Center Steyr | Josef Weber, University of Applied Sciences Munich | |||
14:30 CEST | Advancement in fatigue prediction in threaded fasteners and components | 13:30 CEST | Academic award presentation - Impact of microstructural features on the fatigue strength of cast alloys by means of a layer-based approach | |
Richard Tichy, AVL List GmbH | Matthias Oberreiter, Montanuniversität Leoben | |||
15:00 CEST | Design accompanying & customized fatigue assessments with FEMFAT inside ANSYS at Palfinger | 14:00 CEST | Question & answer / Best lecture award / Farewell | |
Dr. Felix Koch, Palfinger Europe GmbH | Dipl.-Ing. Helmut Dannbauer, Dipl.-Ing. Klaus Hofwimmer and Dr. Christian Gaier, Magna Powertrain Engineering Center Steyr | |||
16:00 CEST | Random vibration analysis of a piston compressor | |||
Viktor Jakab, Knorr Bremse | ||||
16:30 CEST | Structural validation of printed circuit boards with FEMFAT MELCOM | |||
Christian Neubacher, Magna Powertrain Engineering Center Steyr | ||||
17:00 CEST | Dynamic contact simulation for fatigue analysis: new mobility truck rela-ted use cases | |||
Dipl.-Ing. Markus Breitfuss, Magna Powertrain Engineering Center Steyr | ||||
17:45 CEST | Guest lecture - Invention in the AI age | |||
Bruno Buchberger, Johannes Kepler University |
Events & Training
In the second half of 2025, we once again offer a wide range of events:
- Simulia Regional USER Meeting - Eurocentral 2025 – Bamberg (Germany)
- Magna ECS Simulation Conference – Waidhofen / Ybbs (Austria)
- NAFEMS World Congress 2025 – Salzburg (Austria)
- EVTeC 2025 – Yokohama (Japan)
- DVM Strukturfestigkeit und Produktlebenszyklus – Berlin, Gutshaus (Germany)
- CADFEM Conference Künzelsau – Künzelsau (Germany)
- FEMFAT Roadshow – Mageburg (Germany)
- FEMFAT Roadshow – Münster (Germany)
We offer a variety of training programs in 2025:
- Find your Standard Training
- Find your Advanced Training
Transforming Pulsating Load Test Data into Alternating Strength Data for FEMFAT
As part dimensions continue to decrease, it has become more and more common to perform fatigue tests using thin specimens, with thicknesses ranging from 1 to 3mm. However, the fatigue test for fully reversed conditions (stress ratio R=-1) then poses significant difficulties due to buckling problems. As a result, fatigue tests are often conducted under pulsating conditions (stress ratio R=0).
On the other hand, FEMFAT requires information on the S-N curve under R=-1 conditions, including the alternating tensile strength σalt (endurance limit), slope kalt, and cycle limit NC,alt. In other words, the test results from pulsating tests cannot be imported directly in FEMFAT but need prior processing. And that is exactly what this article is about: guiding you through this process.
What you need to know to solve this challenge is that in FEMFAT all S-N curve parameters are adjusted based on the mean stress influence (see Figure 1).
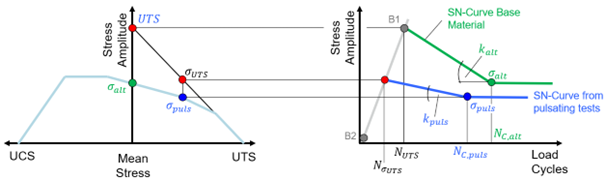
Figure 1: Mean Stress Influence in FEMFAT (blue data are known from pulsating tests, green values should be calculated)
Consequently, the endurance limit for R=-1 conditions can rather easily be inferred through mean stress sensitivity. However, both the slope and cycle limit of the S-N curve under R=-1 conditions require somewhat more complex calculations.
But let’s start with the requirements first: what are the minimum input data from testing in this scenario under consideration?
- Ultimate Tensile Strength (UTS)
- S/N curve data from pulsating test:
- Pulsating endurance strength σpuls
- Slope of pulsating S-N curve kpuls
- Cycle limit for pulsating S-N curve NC,puls
First step: Computation of the alternating strength σalt
Here the mean stress sensitivity M is needed. This value indicates how strongly the mean stress influences the fatigue strength. In the Haigh diagram the mean stress sensitivity is visualized as connecting line between alternating strength σalt and pulsating strength σpuls. For the computation we will use the following relation between mean stress sensitivity M, σpuls and σalt:

To compute σalt from this relation we need M in addition to σpuls. Since in FEMFAT M is a material class specific parameter, we can generate an arbitrary material to identify it. To do so, open the FEMFAT Material Generator, select the appropriate material class and enter the UTS value. If known, adjust the yield strength to the value from test. Calculate the mean stress sensitivity M from the generated values for σpuls and σalt.
Now we can use equation 1, insert the known values M and σpuls to compute σalt.
Second step: Computation of slope kalt and cycle limit Nc,alt
To compute the slope kalt we will make use of the relations depicted in figure 1: the local slope varies along the curve defined by the points B1 and B2. Deflection point B1 represents the range of the pure alternating period test where the stress amplitudes are in the range of the ultimate stress limit. The decrease in the load cycle number as moving to point B2, with a load cycle number 1, can be interpreted as a decrease in the crack-closing bias under high static tensile prestressing.
From figure 1 – please observe the double-logarithmic scale – we get
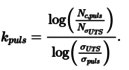
We can rearrange this relation to compute
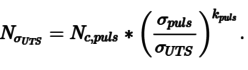
Analogously we get for
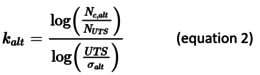
To compute kalt that way we need to know the terms from the nominator Nc,alt and NUTS.
As we already know, the cycle limits under pulsating Nc,puls and alternating conditions Nc,alt are connected by the mean stress influence. FEMFAT uses the following empirical formula to describe this relation (see FEMFAT theory manual):
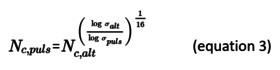
We can rearrange equation 3 to compute
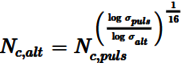
On the other hand, there is a second relation for NσUTS
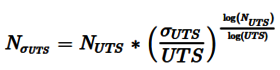
By tedious, but elementary operations we can compute
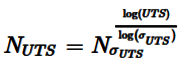
With these relations, the slope kalt under alternating loading conditions can be calculated from equation 2.
In the final step, enter the values in the Material Generator under the S-N data menu and save the material.
Example
Given Data
As an example, we consider an iron material (fine-grained steel), for which the following test data are available:
Formula Symbol | Value | Description |
UTS | 700 MPa | Ultimate Tensile Strength |
σpuls | 560 MPa | Pulsating Strength (R=0) |
NC,puls | 1.9E6 | Cycle Limit (R=0) |
kpuls | 20 | Slope of S-N curve (R=0) |
First step: Computation of the alternating strength σalt
With the material class characteristic mean stress sensitivity M=0.1448 we use equation 1 to compute

Second step: Computation of slope kalt and cycle limit Nc,alt
The cycle limit can be calculated directly from equation 3:
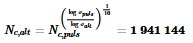
Inspecting equation 2, we see we need to compute the following auxiliary quantities for kalt first:
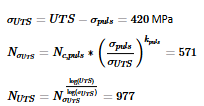
Finally, we get:
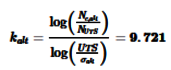
We enter the values in the Material Generator under the S-N data menu and save the material.
As a verification we use this material to analyze the fatigue behavior under pulsating loading condition.
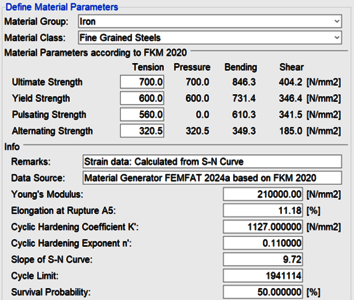
Figure 2: Material Card with the computed R=-1 S-N curve data
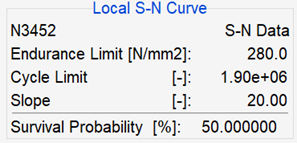
Figure 3: Local S-N curve result from the verification analysis
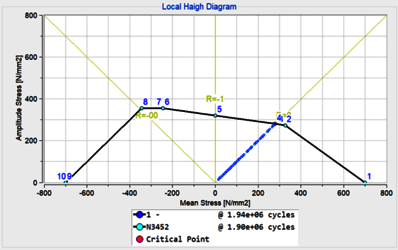
Figure 4: Local Haigh diagram from the verification analysis
We are thrilled to announce the release of FEMFAT LAB 2025!
This latest version comes packed with exciting new features and enhancements designed to streamline your workflow and improve your analysis capabilities. Here are some of the highlights:
-
New MatPro Module: Assess raw material test data with greater accuracy and ease.
-
Automated Measurement Report: Save time with automated generation of measurement reports.
-
CSV Import for PSDs and Transfer Functions: Simplify data import processes with new CSV support.
-
Formula Compiler and Explorer Rework: Enjoy a more intuitive and powerful formula compiler and explorer.
-
Kurtosis Value in Statistic Evaluation: Gain deeper insights with the inclusion of kurtosis values in statistical evaluations.
-
Performance Optimization for Virtual Iteration: Experience faster and more efficient virtual iterations.
And that's not all! There are many more improvements and new features to explore.
The installation package, along with the detailed release notes, is available for download on our new website: femfat-lab.magna.com. Please note that access to these resources is limited to registered and logged-in users.
Frequently Asked Questions
FAQ1: What should be considered when evaluating rotating components from Ansys?
Check Category "Module max" for ANSWER
FAQ2: What Options Do I Have for Efficient Analysis and Evaluation of Base Material, SPOT, and WELD Nodes?
Check Category "General" for ANSWER