
Modules
Learn about our modules
FEMFAT offers various modules such as FEMFAT basic, FEMFAT weld and many more.
Read more about the individual modules below.
If the loading is determined by two dominant loading situations (e.g. upper & lower load case) and one optional constant load, then FEMFAT basic is the ideal tool for fatigue analysis.
The BASIC module enables analysis of the fatigue life or endurance safety of components subject to proportional loading.
The ability to take a great number of possible influence factors into account makes it easier to obtain a realistic fatigue life prediction.
Welds and spot weld connections can be analyzed in the same computational run as the base material.
The range of functions also includes a comprehensive material database with over 400 data sets as well as the so-called material generator for the creation of new material data sets.
Obtaining a fatigue life prediction for multiaxial loading is a great challenge. This is because the superposition of several loads can cause failure-critical total damage amounts to be reached even at locations which are completely inconspicuous under single loads.
Typical multiaxially loaded components (wheel axles, car body structures, etc.) are subjected to loading from different directions at the same time. The forces applied through braking and acceleration, potholes, etc. apply variable loading to the structure.
Consequently, reliable fatigue analysis requires the use of special solution approaches. The methods applied in this case are based on scientific publications, the most recent in-house developments and research studies conducted in cooperation with leading international institutes. All methods, theories and hypotheses have been and continue to be used and validated successfully in countless projects.
The possible analysis objectives in FEMFAT max include damage or fatigue life, endurance safety factors, static safety factors and degree of multiaxiality, separately for every FE node.
You can choose between ChannelMAX and TransMAX depending on the type of load:
With ChannelMAX, load-time signals are combined with the corresponding stresses from the unit load cases in FEMFAT and are superimposed linearly. This makes the simulation comparable to the situation on the test bench where the component is loaded in several directions at once by servo-hydraulic cylinders.
TransMAX is the module of choice if the sequence of the load cases can be described by transient stress distributions. This means that a separate stress result is available for each point in time of the load history. In contrast to the channel-based approach in ChannelMAX, there is no linear superpositioning here. This makes a fatigue analysis possible even when taking non-linear effects into account in the FE analysis.
MAX Advantages:
- Reliable and effective multiaxial fatigue analysis of axle components, suspension systems, car body frames, engine components, bodies in white, etc.
- Interfaces to various different load-time signal formats from multi-body simulations and measurement data software packages
- Channel-based or transient load data definition
- Cutting-plane and node filters for reduced analysis times
- Many different equivalent stress hypotheses
- Fatigue life predictions of short-fiber reinforced plastics including orthotropic material data
- Unlimited number of loading channels
- Ability to compress large histories (shorter analysis times)
- Compatible with FEMFAT weld and FEMFAT spot for simultaneous analysis of the base material, weld and spot joints
- Assessment of continuous fiber-reinforced plastics with LAMINATE (only in ChannelMAX)
- Add-on tools such as Harmonic and Elastoloads for modeling and analyzing vibrational phenomena or elastomeres
Countless spot welds and punch rivets are required in order to ensure the structural strength of a vehicle or a vehicle cab. Because this invariably concerns potential crack initiation sites, particularly reliable methods for fatigue analysis are required.
FEMFAT spot offers precisely those methods that are required for correct stiffness and fatigue life simulation of spot-joined components.
Two different approaches are available for this purpose:
Stress-based assessment
For a stress-based assessment, the individual joints are represented by a detailed shell model optimized for stiffness (nugget model). These nuggets can be generated either in FEMFAT with the integrated remesher module or with a different preproccesor. The advantage of using the remesher or the ANSA preprocessor is the fact of the fully automatic definition that is provided. The next step is the stress analysis of the locally modified model as the basis for the fatigue life prediction. Another possibility for FEMFAT spot assessment is the usage of Nastran Superelement technology. Here, detailed analysis of notch stresses in the joint is possible even for whole car bodies.
Force-based assessment
In this case, the spot weld connections are represented by simple connections (beams + connectors, solid + connectors, CWELD, etc.). The fatigue analysis is based on analytical stresses that are calculated from the internal forces and moments in accordance with the JSAE method, which is an improved version of the well-known Rupp method. The overall analysis times are especially short as compared to the stress-based method, not least because the nugget generation can be omitted. However the results are also more mesh-sensitive.
The centerpiece of the fatigue life prediction for both analysis approaches is a database in XML format that has been adjusted in line with test results and which contains comprehensive fatigue-relevant parameters.
This database also allows flexible definition of connections, e.g. the use of different types of connections (spot welds, rivets) and equivalent stresses in one and the same calculation run or separate material assignments for each sheet of a connection, etc. Moreover, specifically for the analysis of bolted connections, nugget elements with a total of three rows can be created (remesher or ANSA) and analyzed.
FEMFAT spot is available as an influence factor for the fatigue analysis in BASIC, MAX and SPECTRAL and can also be combined with WELD.
Excitation mechanisms with a high level of randomness (e.g. shaker excitation on test benches or road excitation) lead to an increase in calculation effort due to the long time series that become necessary. FEMFAT spectral offers an ideal solution for this. The multiaxial damage analysis is carried out directly in the frequency domain (“Random Response Fatigue”), which dramatically reduces the duration of the fatigue calculation.
To do so, SPECTRAL uses the alternative description of signals in the frequency domain, so-called PSDs – Power Spectral Densities. The multiaxial damage analysis is carried out in the frequency domain.
Similar to a channel-based simulation with ChannelMAX, FEMFAT spectral employs a unit-load-based approach. This considers a unit excitation that is constant over the frequency for each individual load direction. An efficient numerical simulation of these loads is made possible by using a modal frequency response analysis in the frequency domain. The results obtained are the corresponding modal stresses and a set of modal transfer functions per unit load case. From this, SPECTRAL generates the corresponding transfer functions of the local stresses which are then scaled with the power densities of the loads resulting in the overall load which is actually applied.
Due to the fact that in many applications, the loads are not applied completely independently of each other, FEMFAT spectral offers the option of considering phase relationships between the individual loads by defining cross power spectral densities (cross PSDs). The use of cross PSDs offers the additional advantage that the formation of the equivalent stress PSDs can be carried out in a manner that is statistically correct. For the subsequent damage analysis, in addition to the classical cutting-plane method, probability models according to Dirlik or Rayleigh are used.
SPECTRAL Advantages:
- Multiaxial damage analysis for stochastic loads
- Short analysis time due to a numerically efficient and robust simulation process in the frequency domain
- Probability models according to Dirlik, Rayleigh and exclusive mean stress models
- Analysis of different load situations without repeating the FE analysis
- Numerous influencing factors are available, including WELD for simultaneous analysis of the base material and weld seams.
This module makes it possible to calculate safety factors or damage based on measured strain histories as well as to compare measured and simulated strains.
FEMFAT strain is the connecting link between tests on the test bench and virtual structural analysis. Using this module, you can on one hand make local fatigue predictions based on measured strains – an FE model is not even required to do so (STRAIN calc). The second possible application is aimed at the calibration of the model: the strains measured on the real component are compared (graphically) to the values resulting from the simulation (STRAIN comp).
FEMFAT strain is available as an additional analysis target (STRAIN comp) in BASIC and MAX. STRAIN calc is a separate, independent module.
LAMINATE is a module for the analysis of continuous fiber-reinforced plastics and it is only available in ChannelMAX.
The top and bottom of each layer in a composite is subjected to a damage analysis. The analysis method is a version of the “Critical Component in Critical Plane” method which has been adapted for laminates and which considers both fiber breakage and intermediate fiber breakage. Moreover, delamination can also be considered when solid models are used (typically 8-node hexahedrons). Damage analysis requires static (tension and compressive strength) and cyclical material data (S-N curves) for loads parallel and perpendicular to the fibers as well as shear loads in the laminate plane. Shell and solid elements with COMPOSITE characteristic are currently supported from the Abaqus inp and odb file.
Laminate Advantages:
- Multiaxial fatigue analysis of continuous fiber-reinforced plastics
- Analysis of fiber breakage, intermediate fiber breakage and delamination
- Simultaneous analysis of a mixed structure of standard materials (steel, aluminum, etc.) and laminates in a single computation run
- Display of the results (damage, stress amplitude, mean stress, S-N curve, etc.) both for each individual layer and each stress component separately
- Mean stress influence on endurance limit and slope / cycle limit
- General surface treatment factor for all layers
- Statistical influence
This module is for calculating elasto-plastic stresses based on a linear elastic FE analysis.
FEMFAT plast makes use of the Neuber correction to estimate the local elasto-plastic stresses in notches on the basis of linear-elastic stresses. For this application, the Neuber rule establishes a relationship between linear and non-linear stresses or strains. With the Young's Modulus and the non-linear strains, this relationship (“Neuber hyperbola”) can be written as:

Making use of the Ramberg-Osgood equation for describing the cyclical stress-strain curve (with the cyclical coefficient and cyclical exponent of hardening), it is possible to calculate the non-linear stresses as:

the intersection with the Neuber hyperbola.
Consequently, with local plastification, no FE analysis with non-linear material behavior is necessary; the elasto-plastic stresses can also be determined with FEMFAT plast by approximation. This also entails a calculation effort that is reduced accordingly in the FE analysis.
FEMFAT plast is available as an influence factor for BASIC and MAX and is activated by default.
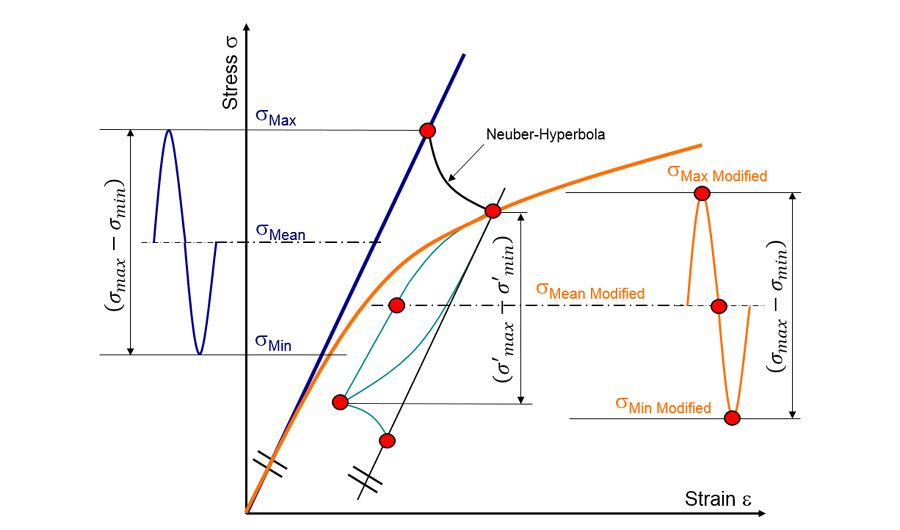
For the modern development of welded structures, a precise fatigue life prediction of these joints has become indispensable. FEMFAT weld assists you with this.
In the determination of the fatigue life or safety factors of welded structures, you can count on the flexibility provided by FEMFAT weld: the methods implemented enable simultaneous analysis of shell and solid models. The tedious, detailed modeling of the weld geometry with fillets for the weld root and weld toe can be omitted entirely. The weld definition can be carried out conveniently in FEMFAT visualizer for shell-shell and shell-solid connections – even independently of the FE analysis.
For the fatigue analysis, the FE structural stresses are scaled up to obtain notch stresses for root and toe as well as for start and end by means of notch factors taken from a database and are then analyzed. The database is provided in ASCII format. Consequently, you can modify the notch factors and material parameters contained there to obtain an even better prediction quality or add new joints.
The SolidWELD method, on the other hand, uses a stress interpolation approach for the analysis. Here, the stresses are determined at a certain depth (which can be specified by the user) using interpolation and are compared to a master S/N curve which is based on many tests. The ANSA and SimLab pre-processors ensure maximum user friendliness by automatically generating the weld joint and all of the definitions required for the WELD analysis. However, the definitions can also be performed with any other preprocessors as well.
The impressive scope of functions in WELD also includes sensitivity analysis for identifying critical weld geometry parameters as well as standards-compliant assessment options, according to BS7608 or Eurocode 3.
The FEMFAT weld module can be used in combination with BASIC, MAX and SPECTRAL.
Thermo mechanical fatigue (TMF) analysis, i.e. fatigue life predictions for components subject to a combination of thermal and mechanical loading, is one of the most challenging tasks in the area of fatigue analysis. With FEMFAT heat, you will be ideally equipped to deal with this challenge.
The aim of TMF analysis is the calculation of damage results for mechanically loaded components subject to high, fluctuating temperature loading, such as in turbochargers, cylinder heads, exhaust manifolds, etc.
FEMFAT heat is based to a great extent on the proven method of Professor Sehitoglu (University of Illinois, USA). It uses the time-dependent distributions of temperatures determined in FE analyses as well as elasto-plastic stresses and strains for fatigue life analysis.
The main advantage of this method is that it takes the three relevant damage mechanisms into account:
- Mechanical damage
- Oxidation damage
- Creep damage
Because analysis of this nature requires additional material parameters as well as temperature dependent material characteristics, the FEMFAT material database has been augmented with a limited number of commonly used materials including all of the necessary material parameters.
If desired we can provide consultancy on the topics of testing and the creation of FEMFAT material cards for materials not contained in the database.
This module allows the calculation of static safety factors
FEMFAT break is the only module that is not oriented to deal with analysis of dynamic loads. Instead, BREAK analyzes the max. elongation for monotonous loading on the basis of linear stresses.
The influencing factors which can be taken into account include stress gradients, material ductility, technological parameter influence, temperature, local material properties as well as surface residual stresses.
FEMFAT break is available as an analysis target for BASIC and MAX.
The VISUALIZER is a fast, interface-independent 3D post processor for the display of FEMFAT results and FE stresses. Moreover, the VISUALIZER also stands out with its functionality in the area of weld definition for shell models.
The VISUALIZER enables the evaluation and documentation of FEMFAT results, such as damage or fatigue life and safety factors. However, the additional output options provided are especially helpful for gaining deeper understanding of the results and how they are to be interpreted. These include all parameters relevant for the FEMFAT analysis (currently over 50), including equivalent stress amplitude and mean stress or the magnitude of the effects of all activated influencing factors on the local S/N curve.
Moreover, for MAX analyses, a graphic chart of the local equivalent-stress histories and damage histories as well as the most damaging channels/modes is also available.
In addition to the classical functionalities of a post processor, FEMFAT visualizer also provides helpful preproccessor functions for the FEMFAT weld module. It enables fast and easy definition of the weld seams. This can be done completely automatically via the WELDseamScanner integrated in the VISUALIZER. Alternatively, the course of a weld seam can be defined on the FE model with just a few mouse clicks. The type of connection (T-joint, overlap joint, etc.) is recognized automatically. Details concerning the weld shape can be defined with the help of visual assistance.
A further useful feature, the 3D screenshot, turns any PowerPoint document into a small post processor: The model and the currently displayed FEMFAT result can be exported from the VISUALIZER and incorporated in PowerPoint. There, however, the structure is not available merely as a static screenshot, but instead as a full-fledged model with a host of possibilities for adapting the view!
There is also an option for automatically dividing the analysis into several parallel processes and running them on the current computer. Parallelization is performed by splitting the analysis group into a given number of equally sized sub-groups and starting the respective number of FEMFAT instances each with a sub-group. The sub-results (*.fps files) are subsequently merged to form an overall results file.
For licensing the parallel fatigue analysis either parallel tokens or regular licenses are used.