
Newsletter
Bleiben Sie verbunden
Bleiben Sie mit unseren Newslettern auf dem Laufenden! Informieren Sie sich über die neuesten Softwareversionen, tauchen Sie ein in die innovative Ermüdungsanalyse mit FEMFAT, entdecken Sie spannende Veranstaltungen und Schulungsmöglichkeiten und erkunden Sie fesselnde Fallstudien. Wir beantworten auch gerne Ihre häufig gestellten Fragen. Entdecken Sie die Welt der technischen Spitzenleistungen!
Zum Newsletter anmelden
Newsletter 29/2020
Release News FEMFAT 5.4.1; Formula Student: The university motorsport racing series for engineers of the future; Application Example for the Elastoloads Tool; FEMFAT User Meeting 2019 in Steyr; 4th FEMFAT LAB User Meeting in China 2019; FAQ 1 & 2
Release News FEMFAT 5.4.1
With FEMFAT 5.4.1, the new FEMFAT (intermediate) version is now available for download.
You can expect a colorful mixture of new functionalities and numerous program improvements. Selected points are briefly introduced below:
As of now, FEMFAT material files (* .ffd) can contain several different material definitions. Advantage: all definitions can be read in at once, the sequential reading of individual ffd files can be omitted.
Some innovations concern the ABAQUS interface: up to now exactly one odb library was installed in FEMFAT for a certain ABAQUS version. This meant that an odb update was required when importing older files. For large files, this process could lead to significantly longer import times. In contrast, several odb libraries can now be installed at the same time. When importing an odb file, FEMFAT automatically searches for the correct library. The support of „Includes“ also deserves special mention. These are processed correctly when importing structural data in FEMFAT. This improvement also affects the NASTRAN interface. As of FEMFAT 5.4.1 CENTROID stresses are also supported.
With some improvements, the VISUALIZER can further expand its position as a user-friendly postprocessor: the display has been expanded to include local node properties such as material, temperature, surface roughness, technological size and range of dispersion. Subwindows with the local detailed results can now also be requested for all selected nodes. These are automatically arranged intelligently so that you do not lose track of them. On the xMCF interface side, an upgrade to version 3.0 is to be reported.
Additional options for stress averaging have been implemented in WELD. As a result, the weld seam evaluation can be carried out, for example, with un-averaged nodal stresses. For greater flexibility, it is now also possible to define parameters for determining the assessment distance in the hot spot method.
The evaluation of short fiber reinforced plastics is now also possible in SPECTRAL.
Some small but fine enhancements concern a rather inconspicuous and nevertheless frequently used application in FEMFAT, the Rainflow Matrix Viewer. This has been fundamentally revised and equipped with new, helpful functions. Among them are picking individual bars of the rainflow matrix (including the result display) as well as standalone option and opening any FEMFAT rainflow matrix files.
New functionalities facilitate the evaluation of results through the automatic identification and group generation of local extreme values and their output in table form in the report file (* .pro).
Formula Student: The university motorsport racing series for engineers of the future
In motorsport, people and materials go to the limit. Issues such as lightweight design, new materials, durability, but also innovative designs (e.g. for the safety cell) are of crucial importance here. The main goal: to be safer, faster and better than the competitor. Where better to show the capabilities of your product, because motorsport is a technology driver. In the first step, the new developments improve the racing cars and after a while can be found in everyday products or series vehicles of the automobile manufacturers.
However, all of these developments also mean that there is always a person, an engineer, who has the idea, developed it and implemented it. Engineers need the opportunity to try and gain experience. This applies both to the process of brainstorming and that of development including (fatigue) simulation. The Formula Student, a worldwide university racing series with compact, self-developed formula vehicles, offers an ideal playground for this.
The special features of this racing series are the regulations. The vehicles developed by the students are divided into 3 categories. In addition to a class for vehicles with an internal combustion engine, there is also a class for vehicles with electric drive and a class for self-driving vehicles.
In order to drive the development of your vehicles at the highest level, we provide FEMFAT to teams from the Formula Student.
We are happy to support teams with our know-how. Using FEMFAT, brakes, wheel suspensions, chassis in the form of tubular steel frames or monocoques made of carbon have already been analyzed and improved in terms of strength, lightweight design and durability.
Many thanks to the teams from Hawks Racing e.V. from Hamburg and the teams from Vienna, Os.Car Racing and TUW Racing for providing some photos of their vehicles.
We look forward to continued good cooperation and wish all Formula Student teams all the best in their further development and exciting races all over the world.

Application Example for the Elastoloads Tool
Typically, there are two ways of considering load-time data in an FE-based fatigue analysis:
- The road load data is integrated in the FE analysis directly. The results in the form of transient stress responses serve as direct input for the subsequent fatigue analysis in TransMAX.
- The FE analysis uses a unit load case-based approach. The stresses are determined according to normalized static unit loads, the specific road load data are initially disregarded. The link with the road load data takes place in ChannelMAX applying the principle of linear superposition.
The first approach does not use the linear superposition principle, nonlinearities such as contact, large deformations can therefore be used in the FE analysis and the subsequent fatigue analysis.
Disadvantages of this procedure are above all to be found in the FE analysis and lie in the considerably high numerical effort, larger amounts of data as well as in the fact that in the non-linear case every road load data has to be recalculated. For these reasons, this procedure is usually limited to short & simple load profiles for reasons of efficiency.
The second option avoids all these disadvantages of the FE analysis and offers the advantages on the side of the fatigue analysis that general, random & almost arbitrarily long load-time profiles can be processed. Another significant advantage is that the FE results can be combined with various road load data in the fatigue analysis.
These advantages are bought by any compromises in accuracy due to the neglect of possible non-linearities.
The FEMFAT add-on tool Elastoloads bridges the gap between the two approaches, allows the use of non-linear FE calculation results without having to sacrifice the efficiency of a ChannelMAX analysis.
The core idea lies in an interpolation method, in which the FE analysis does not follow the original load history, but first calculates neighboring points.
These neighboring points result by placing a grid around the load curve. This results in a rectangular grid in the case of two forces and a cubic 3D grid for three forces. Non-linear FE analyzes are carried out for these discrete grid points. The deformation and stress states are interpolated from the results at the corner points for all times. Grid points that are not required for interpolation do not have to be calculated. This means that unnecessary states in the FE analysis and channels in ChannelMAX can be avoided.
The advantage of Elastoloads is that all the necessary input files for the FE solver or FEMFAT are created automatically. The expanded output options for post-processing in MetaPost are also particularly helpful, as the deformations, superposed stresses and damage can be animated in no time.
The application of a leaf spring is intended to illustrate the use of Elastoloads. As a special feature, a number of non-linearities supported by Elastoloads are included in this example (contact, hyper-elastic material behavior & large deformations).
The external load is applied in the form of displacements in the x, y and z directions. The load curve is discretized with five steps in the x-, eight in the y- and five in the z-direction (see figure above). This results in a total of 25 FE analyzes with theoretically 200 FEMFAT channels. After filtering, 107 channels relevant for the given load histories remain. The results show damage distributions and equivalent stress histories at selected points.
Summary
With Elastoloads it is possible to evaluate non-linear phenomena in combination with any length of road load data with an efficient channel-based approach in ChannelMAX with regard to durability. Due to the high degree of automation, this tool can be excellently included in the global simulation process. A good selection of the level of discretion leads to a reduction in the required FE analyzes and a minimization of ChannelMAX channels. Additional output in the form of a MetaPost session file simplifies the evaluation and enables even deeper insight into the underlying deformation and damage mechanisms.
FEMFAT User Meeting 2019 in Steyr
The 12th International FEMFAT User Meeting took place in Steyr on May 8 and 9, 2019. This time we had moved the event location to the Steyr city hall. Almost 100 FEMFAT users from all over the world accepted our invitation to exchange technical information under the motto "Fatigue analysis of joint connections". In the context of 18 user lectures, the topic was examined from different perspectives. The challenges that were solved with the help of FEMFAT were manifold. On the one hand, different connection technologies such as arc welding, spot welding, laser soldering, 3D printing or adhesives were dealt with. On the other hand the application for complex structures such as buses, trucks or rail vehicles was presented. In addition to the joints, new materials such as fiber-reinforced plastics and 3D printing or the influence of the manufacturing process, e.g. the porosity of cast aluminum or the influence of trimmed edges on electrical sheets were investigated.
This time we were able to win Jürgen Gumpinger from KTM as a guest lecture. He gave us impressive insights into KTM's X-Bow development and its attempts to measure thousands of kilometers of road to generate a virtual road. As in previous user meetings, the best lecture was chosen by the auditorium and awarded the Best Lecture Award. This time the award went to the company Stadler Rail in Switzerland. Matthias Brücker convinced with his presentation about the implementation of an in-house FEMFAT weld database and its application on bogies and car bodies of rail vehicles.
In addition to the new venue, there was another innovation with the ACADEMIC FATIGUE RESEARCH AWARD. This award recognizes scientific work on the subject of fatigue life and durability, as well as applications and further developments in fatigue simulation. The prize was awarded for the first time at the international FEMFAT Usermeeting 2019 and went to Roman Aigner from the Montanuniversität Leoben for his work on numerical modeling of induction hardened surface layers.
The FEMFAT User Meeting is characterized not only by lectures of high professional quality, but also by the many opportunities for personal discussion and getting to know each other during the accompanying supporting program. In addition to the evening events, there was also the opportunity to visit the BMW plant in Steyr or to visit the Arbeitswelt Museum. The FEMFAT User Meeting 2019 was a successful event and I can already point out the next International User Meeting 2021. We will change the format and establish an ECS Simulation Conference, where the user meetings will unite all software products of the ECS (FEMFAT, LAB and KULI) as well as the ECS dynamic conference. We look forward to welcoming you to this conference.
4th FEMFAT LAB User Meeting in China 2019
From May 27th to 28th, 2019 over 100 interested participants from more than 40 companies came together in the Eton Hotel in Shanghai to visit the 4th FEMFAT LAB User meeting. An event where users share their experience with the software, get information about upcoming features and have detailed discussions with local and Austrian experts.
After a brief introduction of the Engineering Center Steyr and FEMFAT LAB, users presented a wide range of topics including investigations of components, sub-systems and full vehicles. It was a pleasure for us to see the great interest and active participation during the concluding Q&A session. During the organized workshop on the second day many complex applications were demonstrated to show the different use cases of FEMFAT LAB. For example the optimization of fatigue test programs or the creation of a virtual 3D road based on road load data measurements even when you cannot digitize the road.
Special thanks to our sales colleague Wenxuan Zhang and his team in Shanghai for the perfect organization of this event and for making all of this possible.
We are already looking forward to engaging discussions and interesting applications using FEMFAT LAB at the next Chinese User Meeting in 2021.
FAQ 1: Treatment of the stresses of parabolic elements from ANSYS * .rst in FEMFAT
In the ANSYS * .rst file, no node-related results (stresses, strains, ...) are saved for the middle nodes of finite elements with parabolic shape functions. So that an analysis of these middle nodes can still be carried out in FEMFAT, the results of the adjacent corner nodes are used to determine values for middle nodes.
For stresses this is done as follows:
- In the first step, the stress tensor at the center nodes is calculated component wise by arithmetic averaging of the stress tensor at the associated corner nodes. This is done immediately after reading the stresses in FEMFAT for each element with element node stresses. As a result, element node stresses are again obtained at the middle node, i.e. if the middle node belongs to several elements, the stress tensor differs from element to element.
- In the second step, FEMFAT requires node-averaged stresses for the base material calculation. These are determined either when the calculation starts (BASIC), when the VISUALIZER is started in the stress data dialog (BASIC) or when scratching (MAX, HEAT, SPECTRAL). The mean stress tensors of each element at the central node are again arithmetically averaged component by component and the node-averaged stresses are obtained for the FEMFAT calculation:
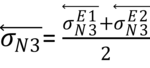
The analogous procedure applies for strains in HEAT. For node results, such as temperatures, the middle node values are read directly from the rst file.
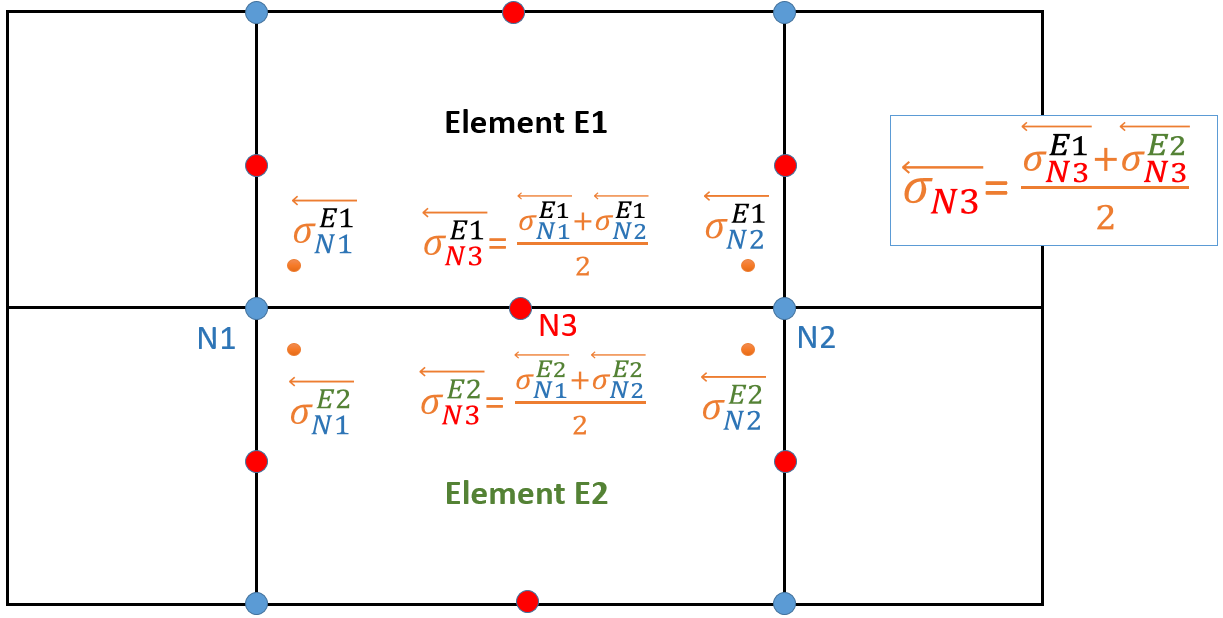
FAQ 2: Loading a job file in a batch job
The default settings regarding influence factors and analysis parameters reflect our recommendations for the fatigue analysis. To follow your own “guidelines” in the department or in the group, you sometimes have to overwrite these defaults. We provided the first help with the templates in FEMFAT 5.1 (2014). They can be found in the FEMFAT installation directory / templates and include the weld sensitivity analysis, the recommended settings for GL 2010 and the evaluation of elastomers. Calling and reading job files is easy with the icon on the graphical user interface , but as such is not recorded in the ffj file. Instead, the read lines are appended to the current job file. In the batch job such a call has to be inserted with the TCL / TK command "source" (the absolut path must be specified or a variable previously defined in the program must be used, as here "installation_path"):
source $installation_path/templates/WELD_Sensitivity_Damage_gap.ffj
The previously described use of variables with the "set" command to assign the "installation_path" the standard installation directory of FEMFAT 5.4 then looks like this:
set installation_path „C:/Program Files/ECS/FEMFAT5.4“
If a job in which another job was read is saved after this action, it is no longer the call of the template or the job that is saved, but the lines from the template! So you have to decide whether you want to keep / save the calculated job files or the previously prepared job file or both. Other TCL / TK commands that make it easier for you to design your jobs with FEMFAT can also be found in the templates for the WELD sensitivity analysis. However, we would like to point out again that manually edited job files are not the standard and can only be examined by our support with additional effort.
BACK TO OVERVIEW